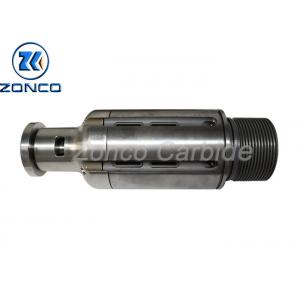
Add to Cart
Tungsten Carbide Coatiing High-Frequency Torsional Impact Generator For Directional Drilling
Working principle:
The upper part of the High-Frequency Torsional Impact Generator is connected with a drill collar or screw, the drill bit joint is connected with the shell, and the lower end is connected with a PDC bit. Both the rotary impact hammer and the commutator of the torsion impact mechanism can rotate to form mutually isolated drilling fluid channels. When the drilling fluid flows through the nozzle under the impact mechanism, a pressure drop is generated. Part of the drilling fluid enters the cavity between the shell and the rotary impact hammer through the slot of the commutator, and drives the rotary impact hammer to rotate. The flow channel leading to the commutator is opened, and the reverse trigger drives the rotary impact hammer to reverse rotation, and the cycle continues to complete the repeated torsional impact in the circumferential direction, so that the PDC bit receives the High-Frequency Torsional Impact Generator while receiving the torque transmitted by the turntable or top drive The 12~25 Hz circumferential impact energy of the device generates additional torque to assist rock breaking, eliminates the "stick-slip" phenomenon of the PDC bit, increases the mechanical drilling speed, and prolongs the service life of the PDC bit.
Product feature of High-Frequency Torsional Impact Generator
1. The use of a torsion impactor can make the drill bit have a longer service life and eliminate the harm caused by stick-slip.
2. It can enhance the reliability of the entire drill string.
3. Greatly improve the stickiness of the hard stratum.
4. Eliminate errors and failures during directional well operations.
5. Reduce the situation of motor failure due to uneven excessive torque.
6. Greatly reduce the number of trips and trips.
7. Save huge cost and drilling time.